-
RitaThe tricone bit quality is good
Diamond Drilling Bit 9-1/2 " PDC Bit Of Oilfield Drilling Tool
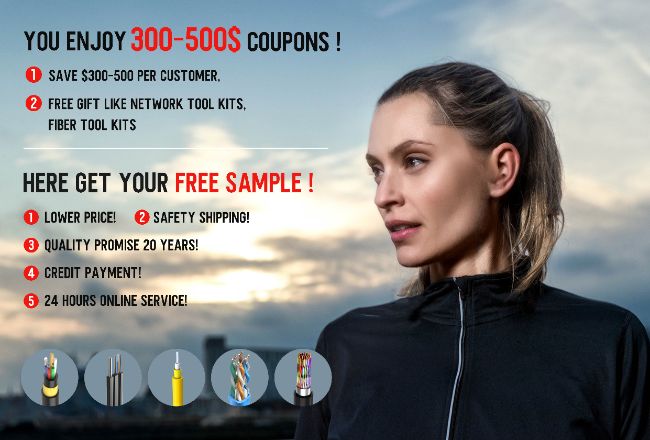
Contact me for free samples and coupons.
WhatsApp:0086 18588475571
Wechat: 0086 18588475571
Skype: sales10@aixton.com
If you have any concern, we provide 24-hour online help.
xUse | Oil Well ,Mining Well ,Water Well ,Geographical Exploration | Primary Cutter Sise | 16mm And 13mm |
---|---|---|---|
Connection Type | API 6-5/8 | API Certification | 7-1548-1 |
Surface Treatment | PDC Cutter Insert | Machine Type | CNC Drilling Industry |
Size | Various Sizes Available | Advantages | Faster Drilling, Improved ROP, Reduced Drilling Costs |
Number Of Blades | 3-6 | Cutter Diameter | 16mm |
Nozzle Qunatity | 9 | Usage | Water Well Drilling,geotechical Drilling |
Application | Oil Well ,Mining Well ,Water Well ,Geographical Exploration | Blades | 6 Blades |
Highlight | Oilfield Drilling Tool PDC Bit,Diamond Drilling Bit,9-1/2 ” PDC Bit |
Diamond Drilling Bit 9-1/2 " PDC Bit Of Oilfield Drilling Tool
1 . Descriptions:
PDC Drill Bits consist of four main components:
- Cutters: Typically cylindrical, with a thin layer of synthetic diamond on a tungsten carbide substrate, used for cutting during drilling.
- Cutting Structure: Often the most complex part of the design, featuring rows of cutters arranged for effective debris removal.
- Blades: With chip flutes between them, serving as channels for drilling fluid to wash away drill cuttings from the bit face.
- Bit Body: The main structure of the PDC drill bit, classified into matrix and steel bodies, connecting to the drill string and supporting the cutting structure.
2. PDC Bit Specification:
Polycrystalline diamond compacts PDC bit in the Oil and Gas Industry PDC bits get their name from the polycrystalline diamond compacts used for their cutting structure. A PDC bit is a drill bit fitted with industrial diamond cutters instead of hardened metal teeth.
SPECIFICATION
|
|
Size : | 9-1/2 " inch (241.3mm) |
Drill Body Type : | Steel Body |
Blades Quantity : | 6 |
Nozzles Quantity : | 6 |
API Connection (in) : | 6-5/8" REG |
Gauge Length (In): | 2 |
OPERATIONAL PARAMETERS
|
|
Weight on Bit (KN): | 22 -112 |
RPM Range(Rotary): | 80- DHM |
Flow Rate(lps): | 29- 38 LPM |
Make-Up Torque(KN): | 16-22 KN.M |
3 . PDC Drill Bit profile
PDC (Polycrystalline Diamond Compact) drill bit is designed, serving as a basis for analyzing, designing, and selecting suitable PDC drill bits. The design encompasses considerations of bit material, cutting structure, PDC cutter type, bit body geometry, and hydraulic system.
PDC drill bits utilize rock shear for drilling and consist of four main parts: cutters, cutting structure, blades, and bit body.
-
Cutters: Typically cylindrical, with a thin layer of synthetic diamond deposited on a tungsten carbide substrate. During drilling, the integrity of the cutter shape is crucial to ensure the bit operates reliably according to its designed 3D geometric cutting structure.
-
Cutting Structure: While seemingly simple, it is often the most complex part of PDC drill bit design. The cutters are arranged in rows to facilitate better cleaning of rock debris. Each row is positioned along the top of the blades, protruding downwards, supporting the cutting structure and maintaining it in place while effectively connecting the cutting structure to the end of the drill string. Between the blades are chip flutes, which serve as channels for drilling fluid to flush drill cuttings away from the bit face as the hole is drilled.
-
Blades: Long blades and short blades are arranged in pairs and staggered along the radial direction of the drill bit. The design of the blades and their arrangement play a critical role in the bit's performance.
-
Bit Body: It can be classified into matrix body and steel body. The interface of the PDC drill bit is made of steel, transitioning to tungsten carbide on the outer surface.
4 . Drill Bit PDC Cutters
Polycrystalline Diamond Composite (PDC) cutters are the main point of contact for a drill bit. PDC bits remove the rock mainly by shearing.
The PDC cutters are exposed to a lot of heating and cooling down the well, a very challenging environment.
PDC cutters that have lower thermal degradation and more thermal stability generally achieve higher ROP and increased wear resistance. So, optimizing the cutter is important.
5. PDC Drill Bit Nozzles
PDC Drill bit nozzles help clear the cutting area and cool the Polycrystalline Diamond Composite (PDC) cutters.
Effective placement of these nozzles along with the angle they are set at plays a critical role on how efficient the drill bit performs.
Fluid channels also complement nozzle placement to improve the clearing of cuttings.
6. Steel Body PDC Bits
Steel body of PDC Bit is the opposite of matrix body. It can of withstanding high impact loads, but is softer and lacks protective features. The strength and ductility of steel give steel-bit bodies high impact resistance.
Steel bodies are considerably stronger than matrix bodies.
A beneficial feature of steel bits is that they can easily be rebuilt a number of times because worn or damaged cutters can be replaced rather easily. This is a particular advantage for operators in low-cost drilling environments.
Polycrystalline diamond compact (PDC) drill bits are different than roller cones in that they are one piece bodies with no moving parts. The fixed-cutters shred the rock, so the bit is able to operate with higher rotation speeds more efficiently in consolidated formations.