-
RitaThe tricone bit quality is good
Oil Drilling Rock Bits 9-1/2 " PDC Drillling Bit Of Diamond Drilling Tool
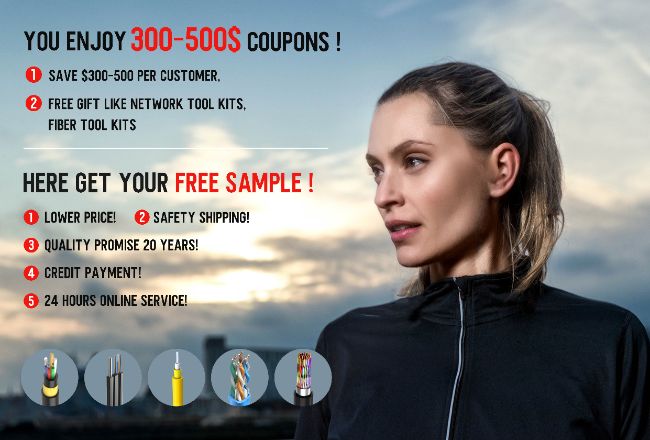
Contact me for free samples and coupons.
WhatsApp:0086 18588475571
Wechat: 0086 18588475571
Skype: sales10@aixton.com
If you have any concern, we provide 24-hour online help.
xApplication | Oil Well ,Mining Well ,Water Well ,Geographical Exploration | Processing Type | Forging,Casting |
---|---|---|---|
Primary Cutter Sise | 16mm | Connection Type | API 3-1/2 |
API Certification | 7-1548-1 | Surface Treatment | PDC Insert |
Machine Type | Drilling Industry | Size | Various Sizes Available |
Warranty | 1 Year | Packing | Steel Box |
Advantages | Faster Drilling, Improved ROP, Reduced Drilling Costs | Number Of Blades | 3-6 |
Cutter Diameter | 16mm | Nozzle Qunatity | 9 |
Usage | Water Well Drilling,geotechical Drilling | Use | Coal Mining / Pcd Impregnated Diamond Exploration PDC Bits |
Blades | 6 Blades | ||
Highlight | Diamond Drilling Tool PDC Drillling Bit,9-1/2 ” PDC Drillling Bit |
Oil Drilling Rock Bits 9-1/2 " PDC Drillling Bit Of Diamond Drilling Tool
1 . Descriptions:
In addition to their core characteristics, design innovations, and wide-ranging applications, PDC drill bits also exhibit several other key features that contribute to their overall performance and effectiveness in the drilling industry.
Enhanced Performance Features:
-
Heat Resistance: PDC cutters are designed to withstand the high temperatures generated during drilling operations, ensuring consistent performance and minimizing the risk of cutter failure
. -
Shock Absorption: The unique design of PDC drill bits allows them to absorb and dissipate the shock and vibration generated during drilling, reducing wear and tear on the bit and extending its lifespan
. -
Customizability: PDC drill bits can be tailored to specific drilling conditions and rock formations, with variations in cutter size, shape, and arrangement to optimize drilling efficiency and performance
2. PDC Bit Specification:
Polycrystalline diamond compacts PDC bit in the Oil and Gas Industry PDC bits get their name from the polycrystalline diamond compacts used for their cutting structure. A PDC bit is a drill bit fitted with industrial diamond cutters instead of hardened metal teeth.
SPECIFICATION
|
|
Size : | 9-1/2 " inch (241.3mm) |
Drill Body Type : | Steel Body |
Blades Quantity : | 5 |
Nozzles Quantity : | 5 |
API Connection (in) : | 6-5/8" REG |
Gauge Length (In): | 1.5 |
OPERATIONAL PARAMETERS
|
|
Weight on Bit (KN): | 9 -67 |
RPM Range(Rotary): | 80- DHM |
Flow Rate(lps): | 29- 38 LPM |
Make-Up Torque(KN): | 9.5 -12.2 KN.M |
3 . PDC Drill Bit profile
The structure of a PDC drill bit is meticulously designed to maximize drilling efficiency and durability. The bit's core components include the bit body, which connects to the drill string, and the blades, which house the PDC cutters.
PDC Bit Body:
- Material: The bit body is typically made from high-strength steel or a matrix material, which provides the necessary rigidity and durability to withstand the forces encountered during drilling13.
- Design: The bit body design can vary depending on the intended application, with features such as fluid passages for cooling and cuttings removal, as well as threads or connections for attaching the bit to the drill string14.
PDC Bit Blades:
- Function: The blades of a PDC drill bit serve as the platform for the PDC cutters, providing the necessary support and stability for efficient cutting action15.
- Design: Blades are usually designed with a specific profile and angle to optimize the cutting action of the PDC cutters, ensuring maximum penetration and minimizing wear16.
- Material: Blades are typically made from high-strength, wear-resistant materials such as tungsten carbide or other ceramic-based composites, which can withstand the abrasive and high-temperature environment of drilling operations17.
- Arrangement: The arrangement of the blades on the bit body can vary, with configurations such as spiral, straight, or a combination of both, depending on the specific drilling application and formation characteristics18.
PDC Cutter Placement:
- Precision: The placement of PDC cutters on the blades is critical to the bit's performance. Precision machining and placement ensure that each cutter engages the formation at the optimal angle, maximizing cutting efficiency and minimizing wear19.
- Spacing: The spacing between PDC cutters is also carefully considered to prevent interference and ensure smooth cutting action, while also allowing for effective removal of cuttings from the wellbore20.
Additional Features:
- Wear Protection: Some PDC drill bits feature additional wear protection, such as hardfacing or wear pads, on the blades and other critical areas to extend the bit's lifespan21.
4 . Drill Bit PDC Cutters
Polycrystalline Diamond Composite (PDC) cutters are the main point of contact for a drill bit. PDC bits remove the rock mainly by shearing.
The PDC cutters are exposed to a lot of heating and cooling down the well, a very challenging environment.
PDC cutters that have lower thermal degradation and more thermal stability generally achieve higher ROP and increased wear resistance. So, optimizing the cutter is important.
5. PDC Drill Bit Nozzles
PDC Drill bit nozzles help clear the cutting area and cool the Polycrystalline Diamond Composite (PDC) cutters.
Effective placement of these nozzles along with the angle they are set at plays a critical role on how efficient the drill bit performs.
Fluid channels also complement nozzle placement to improve the clearing of cuttings.
6. Steel Body PDC Bits
Steel body of PDC Bit is the opposite of matrix body. It can of withstanding high impact loads, but is softer and lacks protective features. The strength and ductility of steel give steel-bit bodies high impact resistance.
Steel bodies are considerably stronger than matrix bodies.
A beneficial feature of steel bits is that they can easily be rebuilt a number of times because worn or damaged cutters can be replaced rather easily. This is a particular advantage for operators in low-cost drilling environments.
Polycrystalline diamond compact (PDC) drill bits are different than roller cones in that they are one piece bodies with no moving parts. The fixed-cutters shred the rock, so the bit is able to operate with higher rotation speeds more efficiently in consolidated formations.