-
RitaThe tricone bit quality is good
PDC Drill Bit 6 Inch Diamond Drill Bit Hard Rock Bit With API 3-1/2 in Pin Box
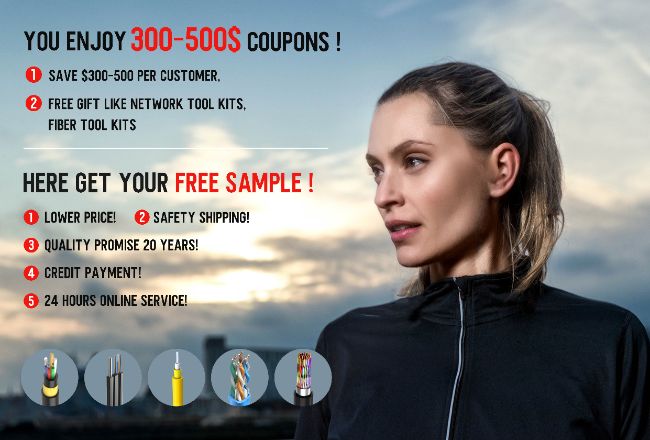
Contact me for free samples and coupons.
WhatsApp:0086 18588475571
Wechat: 0086 18588475571
Skype: sales10@aixton.com
If you have any concern, we provide 24-hour online help.
xType | Pdc Drilling Bit | Use | Oil ,gas ,minig ,drilling |
---|---|---|---|
Material | Diamond ,Alloy Steel ,Tungston Carbide | Machine Type | Drilling Tool |
Processing Type | Forging ,Casting | Application | Rock Drill Of Oil ,mining ,gas |
Size | 6"(152.4.mm) | Color | Customer Requirement |
Advantage | High-efficiency , High Strength | Cutter Diameter | 13mm |
Usage | Oil ,mining ,gas | Blades | 7 Blades |
Market | Global | Packing | Wooden Box Or Steel Box |
Name | Oil Well Drilling Pdc Drill Bit | Rock Formation | F<8 |
Nozzles | 3 | ||
Highlight | Steel PDC Hard Rock Drill Bit,PDC Diamond Bit 6 Inch,Hard Rock PDC Drill Bits |
PDC Diamond Bit 6 Inch Hard Rock Drill Bit With API 3-1/2in Pin Box
1 . Descriptions:
According to the International Association of Drilling Contractors (IADC), the Fixed-cutter bit classification composed of four characters that designate:
- Body material.
- Cutter density.
- Cutter size or type.
- Bit profile
All of our Drill bits are fit for API standard and used in the drilling Industry.
The PDC drill bits size 3~22inch with 3~9Blades are available. And different classification cutter are optional according to your budget .
2. Design Features:
• 3D designed alloy steel body CNC machined for maximum blade and body strength.
• Tungsten Carbide hard facing in critical areas for increased erosion and abrasion resistance.
• Tungsten Carbide Insert (TCI) enhanced gage pads for increased gage protection.
• Parabolic profile is optimized for blade count, cutter quantity and bit stability.
• Force-Balanced PDC cutter locations minimize bit whirl and drill a precise round hole.
• Asymmetric blade design reduces drilling harmonics.
• Blade protection elements are located strategically to maximize bit life. Standard bits have back-up TCI bumpers while "X" bits have back-up PDC cutters.
3. Specification:
SPECIFICATION | |
Size : | 6" (152.4mm) |
Drill Body Type : | Steel Body |
Blades Quantity : | 6 |
Nozzles Quantity : | 3 |
API Connection (in) : | 3 -1/2" REG |
Gauge Length (In): | 2 |
OPERATIONAL PARAMETERS | |
Weight on Bit (KN): | 2-15 kN |
RPM Range(Rotary): | 20-DHM |
Flow Rate(lps): | 11-15 LPS |
Make-Up Torque(KN): | 10.1-11.5 KN.M |
4 . PDC Bit profile
5. Drill Bit PDC Cutters
Polycrystalline Diamond Composite (PDC) cutters are the main point of contact for a drill bit. PDC bits remove the rock mainly by shearing.
The PDC cutters are exposed to a lot of heating and cooling down the well, a very challenging environment.
PDC cutters that have lower thermal degradation and more thermal stability generally achieve higher ROP and increased wear resistance. So, optimizing the cutter is important.
6. PDC Drill Bit Nozzles
Drill bit nozzles help clear the cutting area and cool the Polycrystalline Diamond Composite (PDC) cutters.
Effective placement of these nozzles along with the angle they are set at plays a critical role on how efficient the drill bit performs.
Fluid channels also complement nozzle placement to improve the clearing of cuttings.
7. Steel Body PDC Bits
Steel body is the opposite of matrix body. It can of withstanding high impact loads, but is softer and lacks protective features. The strength and ductility of steel give steel-bit bodies high impact resistance.
Steel bodies are considerably stronger than matrix bodies.
A beneficial feature of steel bits is that they can easily be rebuilt a number of times because worn or damaged cutters can be replaced rather easily. This is a particular advantage for operators in low-cost drilling environments.
Polycrystalline diamond compact (PDC) drill bits are different than roller cones in that they are one piece bodies with no moving parts. The fixed-cutters shred the rock, so the bit is able to operate with higher rotation speeds more efficiently in consolidated formations.
8 .What is the key differences between Roller cone and Fixed Cutter Drill Bits?
Generally speaking, there are two different categories of drill bits, Roller cones and Fixed cutter bits.
- Roller cone bits have rollers rotating around bearings. Roller cone bits use steel teeth or tungsten carbide inserts as cutting elements.
- Fixed cutter bits use diamond cutting elements to fragment the rock. Most types of fixed cutter bits are polycrystalline diamond compact (PDC), natural diamond (mills), and diamond impregnated bits.
- A fixed cutter bit’s life depends mainly on the wear of the diamond cutters while roller cone bits life is generally limited by bearing life rather than cutter wear.
- When properly selected for the formation to be drilled, a fixed cutter bit usually will have a longer life than a roller cone bit, and in general PDC bits drill faster.
- PDC bits remove the rock mainly by shearing, whereas natural diamond and impreg bits drill mainly by plowing and grinding the rock. A roller cone bit removes rock by crushing, gouging and scraping.
- Roller cone bits are made up of three legs welded together.
- Each leg holds a rolling cone fitted with teeth or inserts. Teeth are milled directly in the cone where tungsten carbide inserts are pushed in holes that are drilled in the cone.
- Roller cones that have teeth milled into them are called tooth bits. These steel teeth are brazed over with a protective hard facing which substantially increases the life of the bit. Steel tooth bits are mainly used for fast soft rock applications like surface bits or shallow wells. When the cutters are made from tungsten carbide inserts, the bit is called a TCI (tungsten carbide insert) bit. TCI bits are more durable but are not as aggressive as a steel tooth bit. TCIs are used in harder more abrasive applications.